At its core, CNC milling involves the elimination of product from a work surface through a collection of coordinated movements. Once the style is completed, the driver uses computer-aided manufacturing (CAM) software program to convert the CAD model into a set of instructions that the CNC device can check out, usually in the type of G-code.
One of the standout features of CNC milling is its adaptability. Unlike typical milling equipments, which commonly run along one or 2 axes, CNC milling devices can operate numerous axes simultaneously-- frequently 3, four, and even five. This ability permits manufacturers to accomplish a lot more intricate geometries than ever previously. A three-axis milling equipment can relocate along the Y, x, and z axes to produce a selection of shapes, while a five-axis maker can turn and turn the work surface, enabling accessibility to challenging angles and surfaces. This versatility not only boosts layout opportunities however also improves the production procedure, as it minimizes the need for numerous arrangements and comprehensive manual treatments.
Check out cnc milling guide the transformative globe of CNC milling, a technology that integrates accuracy and automation to generate top quality elements effectively from numerous products, and find its processes, benefits, and key considerations for success in modern manufacturing.
The option of devices is another vital element of CNC milling. The appropriate tool choice can greatly influence the high quality of the finished item and the performance of the machining process.
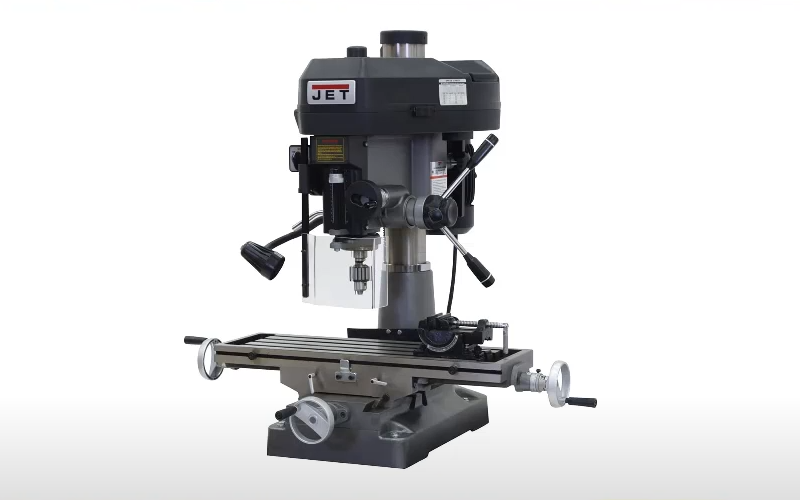
One vital factor to consider in CNC milling is material compatibility. Comprehending the buildings of the product, including its hardness, machinability, and thermal conductivity, allows drivers to maximize the milling procedure and accomplish exceptional results while minimizing wear and tear on devices.
Past the technical elements like style, tooling, and products, there are additional considerations for enhancing CNC milling procedures. Task planning is crucial, as it includes every little thing from machine selection and setup to organizing and operations management. Reliable work preparation can lead to higher effectiveness, lowered preparations, and enhanced overall performance. Using sophisticated attributes such as toolpath optimization techniques can streamline the milling process additionally, enabling quicker machining cycles and lowering waste.
One of the significant benefits of CNC milling is the capacity to automate recurring jobs, which lessens human error and enhances manufacturing uniformity. While traditional milling equipments need a competent driver to look after the production procedure, CNC milling devices can run neglected, carrying out pre-programmed guidelines with precision. This degree of automation not only enhances performance but likewise liberates skilled workers from mundane jobs, permitting them to concentrate on even more beneficial tasks such as quality assurance and procedure enhancement.
In spite of its advantages, transitioning to CNC milling is not without obstacles. The accessibility of leasing choices and inexpensive entry-level CNC milling equipments has made it a lot more easily accessible for little and mid-sized organizations to embrace this technology.
Training and ability growth for personnel running CNC milling devices are also vital for optimizing the return on investment. Operators require a solid understanding of both the CNC maker itself and the software being utilized for programs and surveillance. Many producers discover success by supplying internal training programs or partnering with external training companies to outfit their teams with the essential skills and understanding.
In current years, technological innovations proceed to shape the field of CNC milling. As sectors progressively turn to automation, integrating attributes such as artificial knowledge (AI) and machine discovering right into CNC devices can better improve the precision and effectiveness of milling procedures.
Moreover, developments in software program are continuously tightening the gap between style and production. Modern CAD/CAM systems now supply extra instinctive interfaces and improved simulation capabilities, enabling drivers to picture machining procedures prior to they are implemented. By spotting potential issues in the design stage, companies can resolve layout problems or optimize reducing techniques without sustaining expensive changes to physical materials.
In the context of CNC milling, sustainability is additionally acquiring value as manufacturers seek means to reduce their ecological effect. Implementing methods such as optimizing cutting parameters, making use of more effective tooling, and recycling products can contribute to a much more lasting milling procedure. In addition, innovations such as additive manufacturing are being explored along with CNC milling, presenting possibilities for hybrid manufacturing strategies that even more improve sustainability by reducing waste.
Explore benchtop milling machine the transformative globe of CNC milling, a modern technology that integrates precision and automation to create premium components successfully from different materials, and find its procedures, benefits, and crucial factors to consider for success in contemporary manufacturing.
Finally, CNC milling represents a crucial asset in contemporary production, offering business with the capacity to produce complicated and high-grade components effectively. Its combination of automation, flexibility, and precision has actually made it a staple in markets ranging from aerospace to automobile, medical to customer items. Comprehending CNC milling starts with a strong foundation in its procedures, including the interplay in between style, tooling, products, and software application. As technology remains to evolve, the possibility for competent operators to take advantage of these advancements will just expand, enabling for better efficiencies and technologies in CNC milling applications. By staying notified on ideal practices and emerging innovations, suppliers can position themselves at the forefront of this dynamic market and totally manipulate the capacities that CNC milling uses. Eventually, successful integration of CNC milling equipment, skilled workforce training, and smart automation leads the way for the future of production, where quality, efficiency, and sustainability come to be the trademarks of functional excellence.